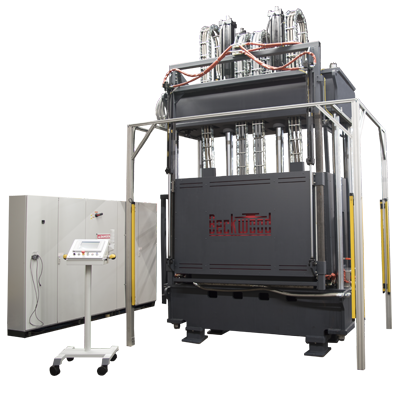
St. Louis, MO – Beckwood Press Company, a leading manufacturer of custom hydraulic and servo-electric presses, automation systems, and the Triform line of precision forming equipment, has partnered with a Midwest aerospace parts supplier to design and manufacture a 150-ton hydraulic press used to hot form titanium structural components.
Capable of temperatures up to 1600°F, the custom forming solution uses electric cartridge heaters to provide even temperature distribution throughout the forming process, increasing the malleability of titanium and reducing springback. Utilizing nine zones of heat control in each platen, operators can maintain a constant platen temperature to within +/-5°F throughout the cycle. An automatic insulated door system increases heat efficiency and maintains the desired temperature set points while facilitating easy part and tool loading.
To counteract the effects of off-center loading and die warpage due to the high temperatures, Beckwood included their proprietary Active Leveling Control (ALC) technology. ALC uses a high-speed motion controller, linear transducers, and proportional valves to synchronize the press’ actuators and maintain bed-to-ram parallelism throughout the cycle.
Like all Beckwood presses, the structure is designed to the Infinite Life classification using Finite Element Analysis (FEA) software. The computer-aided simulation, which mirrors real-world manufacturing stresses, ensures the press is robust enough to handle the most taxing applications. Additionally, Beckwood’s PressLinkTM remote support module offers fast, complimentary troubleshooting and facilitates program updates without the need for an on-site service visit.