What are the parts of a press?
Hydraulic presses and servo-electric presses are complex pieces of equipment, each of which contain many moving parts. The parts of a press can vary depending on press type and frame style, but some components are universal to all press technology. Understanding the components of a press and the terminology used by your OEM will ensure you get the exact specifications needed to make successful parts with your new hydraulic press. Below are a few of the most common terms used to describe hydraulic presses and servo-electric press machines, what they do, and some additional terminology to help you have more meaningful conversations with your OEM.
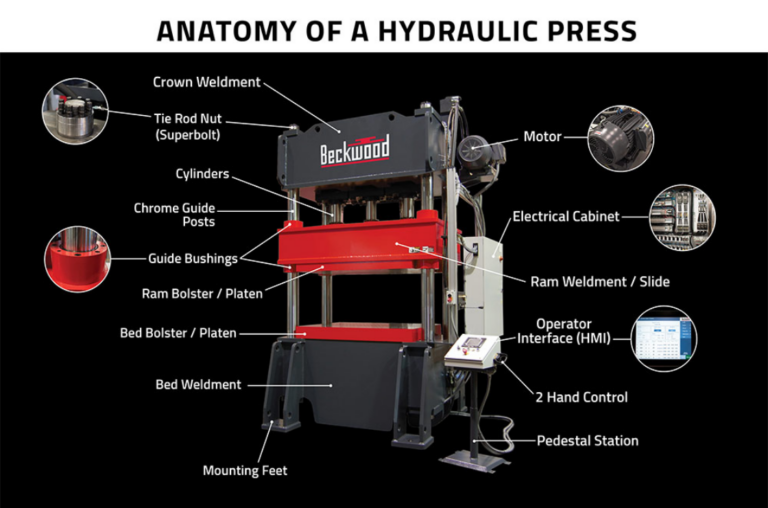
Parts of a Press
Bed
The press bed is the flat, stationary, machined surface that supports the lower bolster or dies.
Bed Cushion
Commonly required for deep draw applications, a bed cushion is used to apply resistance force when pushed upon. This resistance force ensures the material is drawn smoothly, without wrinkling or tearing. Bed cushion force can be dynamically controlled throughout the stroke, allowing the resistance force to change based on the position of the bed cushion.
Bolster
The bolster is the removable plate that serves as the working surface of a press. The plate is typically bolted to the bed and ram weldments. Tooling is attached to the bolster, which can feature a variety of work-holding features such as T-slots, drilled and tapped holes, lift rails to accommodate quick die change systems, and more.
Bushing
Found on post-guided presses, the bushing is a fixed or removable cylindrical metal lining used to guide the ram and reduce friction. Graphite-impregnated bronze bushings that do not require external lubrication are the longest-lasting type of bushing- which is the only kind that we use here at Beckwood.
Crown
The crown on a press is the upper structural weldment containing cylinders that drive the motion of the ram.
Cylinder
The cylinder is the main actuator of a press. This mechanical actuator converts pressure into linear movement, creating force.
Gibs
Gibs are adjustable mechanisms that guide the reciprocating motion of the ram to ensure squareness and parallelism throughout the cycle. Gibs are usually provided with replaceable liners and are adjustable front-to-back as well as left-to-right to enable the setting of proper clearance and to compensate for wear.
Heated Platen
Heated platens are steel plates to which the press’s tooling is attached that are heated using water (steam), oil, or electricity. These systems usually require thermal breaks (insulation) between the platens and the press structure. Heating controls can be separate or fully integrated into the press control system.
Human-Machine Interface (HMI)
A Human Machine Interface (HMI) is a programmable touch screen computer that initiates the press cycle, monitors press health, and logs critical data and cycle parameters. It is the user’s main control panel for press operation. Beyond standard press operations, the HMI can be used to store and retrieve cycle recipes, either using local storage or network access.
Hydraulic Power Unit (HPU)
The Hydraulic Power Unit (HPU) on a press is a system comprising the tank, motor, hoses, pumps, and chillers that work in unison to create pressure. It is the mechanism that applies pressure to drive motors, cylinders, and other parts of the system. HPUs are typically either skid-mounted or crown-mounted on the press, depending on the footprint requirements.
Motor
The motor on a press is the electric machine that transforms fluid energy into rotary energy.
Platen
Platens are the steel plates, sometimes heated, that are attached to a moving or stationary press member.
Pump
A pump is the device that converts mechanical force and motion into hydraulic fluid power.
Ram
The ram (or slide) is the middle weldment on a press that slides within the frame to create pressure on the tool or die. The ram can move vertically or horizontally depending on the press configuration. Some multi-action presses even have multiple rams for complex forming processes.
Ram Knockout
A ram knockout is an ejection device required by many press operations that strips the formed part from the punch or die.
T-Slot
A t-slot is a notch machined into the platens of a press to hold the die in place. This work-holding feature also facilitates quick die changes.
Tie Rod
Tie rods on a 2-post or 4-post press are long rods with threads and nuts on both ends that hold the frame members together. These rods are stretched to place the frame members under compressive load.
Transducer
A transducer is a device that measures the linear position or pressure of the ram or cylinder rod.
At Beckwood, we source only the highest quality components for
your hydraulic presses and servo-electric press machines.
Speak with our team today to find out more.
Cycle
A typical press cycle is the complete movement of the ram, from the initial start position back to the same start position, that may include feeding and removal of the material or workpiece(s).
Dwell
Dwell is the amount of time required for a press to maintain pressure during a cycle. This is typically accomplished by using pressure lock valves or variable volume pumps that are remotely controlled during long periods of precise pressure holding. Some presses use pneumatic dwell systems, powered by a pneumatic pump integrated into the hydraulic circuit, to reduce noise output and energy consumption.
Ram Speed
Ram speed on a hydraulic system is the total time it takes for the ram to move from the open to the closed position, measured in IPM (inches per minute). Speed is also commonly measured at the three distinct stages of the stroke:
• Fast Approach Speed lowers the ram quickly during the portion of the stroke that does not require any force.
• Pressing Speed lowers the ram quickly during the portion of the stroke that does not require any force.
• Stripping/Retract Speed is after the Pressing portion of the stroke is completed, when the ram retracts at a
Fast Retract speed which affords little force.
Return on Pressure
Return on pressure is a programmable cycle parameter that uses an adjustable pressure sensing device (transducer) to determine the desired maximum pressure to be achieved by the ram. Once this pressure is achieved, the ram completes the cycle by returning to the “Home” (or “Up Limit”) position.
Return on Position
Return on position is a programmable cycle parameter on a press that uses a position sensing device (transducer) to determine the desired position to be achieved by the ram. Once this position is achieved, the ram completes the cycle by returning to the “Home” (or “Up Limit”) position.
Stroke Control
Most presses feature Adjustable Retract Limit Switches to restrict the retract distance of the ram (also known as the “Up Limit” Position). Using only the required stroke for part loading and unloading can shorten cycle times. Other programmable limits may include: Slow Down Limit for deceleration from Fast Speed to Slow Speed; Bottom Stop Position and/or Bottom Stop Pressure.
Our press machinery features unrivaled programmability features and the most advanced HMI available today. SEE FOR YOURSELF
PRESS FEATURES AND SUPPLEMENTAL TERMINOLOGY
Bed Height
The bed height on a press machine is the distance from the bottom of the press structure to the working height or the top of the bed bolster. If a press requires a pit, the working bed height could be defined as the distance from the floor to the top of the bed bolster.
Daylight
Also commonly known as the open height of a press, daylight is the distance between the bed bolster and the ram bolster when the ram is fully retracted.
Deflection
Deflection is the amount of deviation from a straight line that occurs when force is applied to the structure of a press. In c-frame press designs, this is often referred to as yawning, and expresses the amount a frame flexes under a load.
Finite Element Analysis (FEA):
Finite Element Analysis (FEA) is a computerized method for predicting how a press’s structure will react to real-world forces such as vibration, heat, fluid flow, etc. Performed during the press engineering phase, FEA works by breaking down a real object into finite elements and using mathematical equations to predict the behavior of each element.
Footprint
Footprint refers to the amount of space that the press machine occupies on the shop floor after final installation.
PSI
PSI is an abbreviation for Pounds per Square Inch, a unit for measuring pressure in a hydraulic press.
Shut Height
Shut height is the distance between the bed bolster and the ram bolster when the ram is fully extended. This is commonly known as the “Closed Height.”
Stroke
Stroke is the total distance the ram can travel, from full extension to full retraction.
Throat Clearance
On c-frame (gap-frame) presses, the throat clearance is the distance from the vertical centerline of the bed to the back of the press behind the bed. This measure is required to determine the diameter of parts and tools that can be positioned within the press.
Tonnage
Tonnage is the maximum amount of force a press machine can exert, typically called out in U.S. tons.
Weldment
Weldments are structural components formed by welding together steel plates. Most modular presses have three main weldments: crown, bed, and ram.