The ability to react quickly to new part orders or develop new parts quickly is an integral component of modern manufacturing. Beckwood offers a suite of unique technologies that cater to low volume / high mix forming operations, research & development groups, and LEAN manufacturers alike.
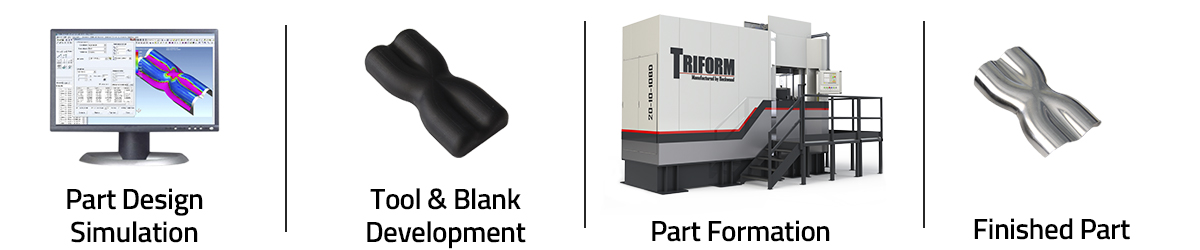
Beckwood’s arsenal of rapid prototyping tools includes:
- Forming Simulation Software
- Sheet Hydroforming Presses
- 3D Printed Tooling
Imagine the following Scenario:
It’s 2:30 in the afternoon and a new part order arrives in your company’s inbox with a delivery timeline of “ASAP.”
You upload the part drawing and material specifications into the Pam-Stamp 2G forming simulation software. Over the next 2 hours, the tooling design, blank design, and forming process variables are simulated, refined and simulated again. The tendency for the material to tear is addressed by modifying the model, and the ideal pressure for preventing a problem wrinkle is found—without wasting a single blank.
It’s 4:30 p.m. and you’re ready to make your tool and cut your engineered blanks.
The tool design generated within Pam-Stamp is sent to your in-house 3D printer. The printer immediately goes to work, adding layer-after-layer of high-performance material, designed to withstand the forming pressures associated with sheet hydroforming. The print job continues into the night and by the time you return the next morning, the tool is ready.
After removing the tool from the printer and gathering your new blanks, you load them into your Beckwood Triform sheet hydroforming press. Applying the programming suggestions from Pam-Stamp, you cycle the press with the confidence of someone who has formed this part before. The tool and blank designs which were optimized during the simulation process perform as planned.
You remove the net shape part from the press after a single cycle. It’s 8:30 a.m. and you’re ready to send the finished part to your customer.
Make this Scenario a Reality for Your Operation
Forming Simulation Software
Beckwood is an official supplier of the Pam-Stamp 2G forming simulation software, by ESI. Pam-Stamp allows users to verify their forming process prior to tools being manufactured, blanks being cut, or the press even being cycled. These simulations offer “experience in a box,” giving users the ability to quickly discover process variables. The result is significantly reduced part development costs, and an expedited part development process.
Get a Free Consultation about Pam-Stamp
Sheet Hydroforming
Sheet hydroforming presses use inexpensive, un-mated tooling to create net-shaped parts with complex geometries in a single cycle. Triform presses offer up to 10,000 PSI of evenly-distributed forming pressure which can result in less than 10% variation in blank-to-finished-part thickness due to uniform elongation of the material. The multi-directional forces applied during the cycle draw the material around the tool smoothly and evenly which reduces thinning and allows you to decrease the thickness of your starting material.
Learn more about Sheet Hydroforming
3D Printing (Additive Manufactured Tooling)
With 3D printing, manufacturers across the world are applying additive manufacturing for a variety of processes. One application that is closely related to Beckwood’s core product offerings is the 3D printing of press tooling. Use of additive-manufactured tooling can help expedite new part development and greatly reduce expenses. The combination of Beckwood Presses and 3D printed tooling is game changing for those manufacturers looking for a competitive edge.
Talk to an engineer about adding 3D Printing to your operation