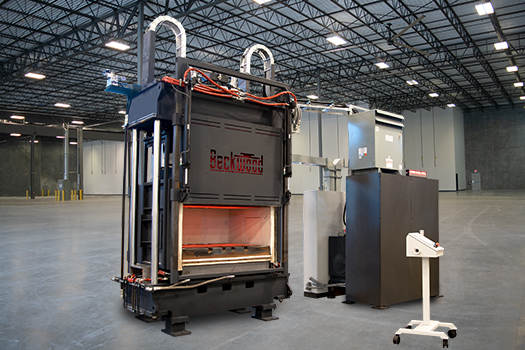
Quick Facts
Type of Press | 4-Post Hydraulic Hot Forming / SPF Press | ||
Tonnage | 400 Tons | ||
Industry | Aerospace | ||
Challenge | Ensure operator safety. | ||
Solution | A robust safety system which includes automated insulated doors, light curtains, perimeter guarding, lockout controls, and flame-resistant hydraulic oil allows users to operate the machinery with minimal PPE at temperatures up to 1300-deg. F. | ||
Challenge | Maintain consistent forming temperatures across the platens. | ||
Solution | Multi-zone electric heaters provide temperature uniformity, to within +/-25 deg. F and allow the user to program temperature offsets across the length and width of the platen. To minimize heat loss and increase energy efficiency, the press uses automated, insulated doors which create a tight seal during the cycle and can cam outward simultaneously or independently depending on the process requirements. | ||
Results | Today, Pryer Aerospace operates two Beckwood hot forming presses to accommodate their growing buisness segment. |
Pryer Aerospace, a leading provider of structural components, assemblies, and kits for the aerospace industry, wanted to overcome barriers to hot forming titanium. For years, they specialized in fabricating complex sheet metal components, many of which are made from titanium, for commercial, corporate, and military aircraft.
When a major customer approached Pryer and made hot-formed parts conditional to winning a large contract, they knew they needed to act fast. “We did every other type of metal forming for aerospace, but hot forming was the missing piece of our overall capability,” says Scott Pryer, former president of Pryer Aerospace.
In 2017, Pryer contacted Beckwood to learn more about the hot forming process and the machinery required to successfully form titanium parts. He quickly learned that the perceived barriers of entry into the hot forming market weren’t as cumbersome as originally thought.
While their first 150-ton hot forming press was being constructed, Pryer and his team visited Beckwood’s facility and operated a similar machine. “By getting to see a hot forming press in person and test it myself, I learned that my earlier perceptions were incorrect,” added Pryer. “Safety really wasn’t an issue—and that was a game-changer.”
Pryer wore an overabundance of safety equipment on day one and quickly discovered that the press’ safety features and overall usability provided much of the protection his team required. By the end of day two, he chose to work with just gloves, safety glasses, a clear face shield, and a long-sleeved shirt, finding that additional safety gear was prohibitive and unnecessary.
During his visit, Pryer also learned that his facility was already equipped to run and maintain a hot forming press, and he wasn’t required to obtain any special approvals to bid on hot forming projects with OEMs or Tier 2 aerospace suppliers.
“I expected to find a surprise complication that would justify our fears, but it never happened. Instead, I found that our company already had a point of reference, so the hurdles were pretty low.”
Explore Beckwood’s Hot Forming and Superplastic Forming Press Solutions.
Download Beckwood’s Beginner’s Guide to Hot Forming Titanium white paper.