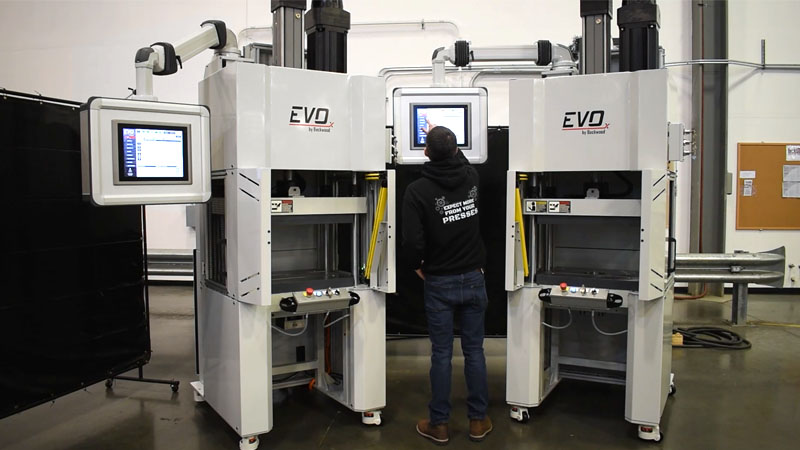
Hydraulic presses may be at the core of what we do, but Beckwood is more than just a hydraulic press manufacturer. As metalforming leaders, we sometimes have to do things a little differently to push the boundaries of our industry. To deliver better performance, better reliability, and better daily efficiency for your pressing needs, Beckwood proudly presents servo-electric presses. With these dynamic machines in your arsenal you can save time, money, and manpower every single day.
Slash Scrap with an Electric Beckwood Press
Of all the press options available at Beckwood, servo-electric presses offer the greatest forming accuracy and precision. This is due to the advanced control capabilities facilitated by the electro-mechanical actuators used in servo-electric presses.
The rigidity of electro-mechanical actuators allow our electric presses to form parts and components within extremely tight tolerances. With positional repeatability within +/- 0.0005” and force control within +/- 0.5%, there is no doubt that servo presses are better equipped for high precision operations than hydraulic and servo-mechanical presses. These excellent forming capabilities boost production quality overall, leading to less scrap and increased product output.
Another clear benefit of electric presses over hydraulic presses is the elimination of hydraulic fluids. There are a few process risks to consider when utilizing a hydraulic press for your forming operations, such as part contamination. When using hydraulic fluid there is always a possibility of a fluid leak. Whether the leak originates from the fluid reservoir or a process line, any fluid leak may very likely contaminate a part formed by the press. When using an electric press, this risk is completely removed, which greatly reduces part and material scrap.
Being able to provide full tonnage throughout the stroke is another advantage that electric presses have over servo-mechanical presses. Servo-mechanical presses have diminishing force capabilities the further the ram is from bottom-dead-center (BDC). This often requires mechanical presses to be over specified in tonnage to allow for effective work above the BDC. This increase in machine tonnage results in not only higher machine prices, but also foundation, rigging and long term maintenance costs.
From hot forming to deep drawing, the LSP can tackle your aerospace forming needs.
Contact us today to learn more and get in touch with our Solutions Team.
Contact Beckwood Press
Servo-Electric Presses Use Less Energy
While traditional hydraulic presses may have a lower up-front cost than servo-electric presses, you may see those costs equal out or even swap over time as hydraulic presses have far higher energy consumption across the board.
A difference in energy expenditure, which is not often considered, is the difference in heat generated by each press. In traditional hydraulic presses, fan or water based cooling systems are necessary to maintain the hydraulic oil at optimum temperatures and not to overheat. These cooling systems require additional energy to operate. Servo-electric presses do not require cooling systems and thereby eliminate both energy costs and maintenance costs associated with maintaining these systems.
The largest contributor to the difference in energy efficiency between hydraulic and electric presses is the way that each press behaves when idling. Even between stroke cycles, hydraulic presses continuously consume energy. Some technologies have been developed to mitigate energy waste in hydraulic presses like variable frequency drives, pneumatic dwell systems, and soft starters; however, these tools still do not bring hydraulic presses down to a level of energy consumption comparable to electric presses.
On the other hand, servo-electric presses only draw energy when it is called for- meaning that the only time your servo-electric press will consume energy is when it is actively being used to form a part. This makes electric presses much up to 50% more energy efficient than hydraulic presses.
Subsequently, this results in significant cost savings as well- up to 70%. These cost savings can expedite your ROI, making the investment in a servo-electric press well worth considering.
Minimize Maintenance with an Electric Press
Although hydraulic presses are robust and reliable, accidents sometimes happen. Machine maintenance can require a high attention to detail, as hydraulic systems have many intricate components. This includes hydraulic fluid lines, which have the added risk of creating a workplace hazard if the fluid were to leak out of the system due to press malfunction or mishandling. Whether spontaneous or scheduled, any kind of maintenance or repair on a hydraulic press can result in significant process downtime.
Compared to a traditional hydraulic press, Beckwood’s servo-electric presses employ up to 80% less individual machine components. With no hydraulic systems, no flywheels, and no mechanical crankshafts, potential failure modes are exponentially reduced in electric presses. We also use roller screw actuators, which can extend the life of a press by as much as 15 times when compared to more commonly used ball screw actuators. These design improvements drastically reduce the need for routine maintenance- users can get millions more cycles out of an electric press before any form of maintenance is required.
When maintenance and repair time does eventually come around, working on an electric press is quick and simple thanks to our lean system design. There are no hydraulic fluid lines to worry about, just standard mechanical and electrical components. Parts like servo controllers, small servo motors, and drive systems are easily sourced from any standard component supplier. We make sure that the parts used in our electric presses are easy to source.
If an electric press sounds like the right fit for you, reach out to Beckwood today. Our dedicated Solutions Team can develop electric presses to meet the needs of any tonnage, any industry, and any application. Soon enough, your business can become our next success story.
Expect more from our presses.