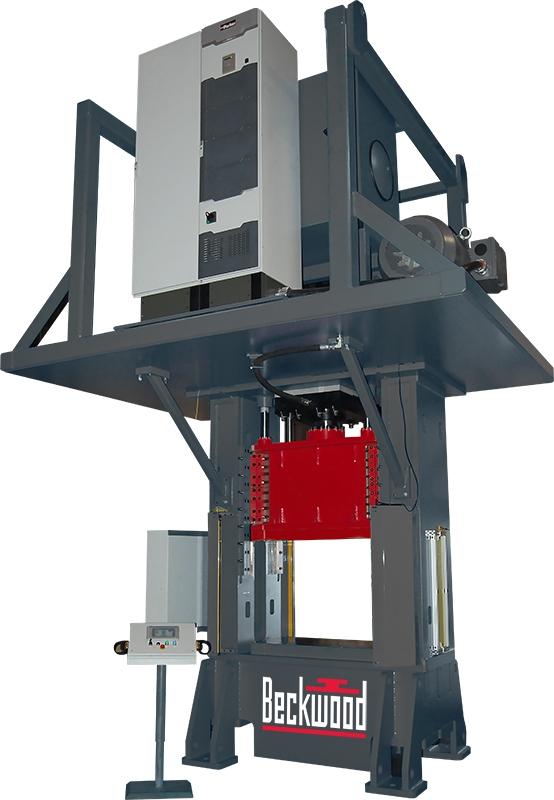
Forging presses are some of the world’s earliest metalworking machines. Historically performed by blacksmiths using a hammer and anvil, forging has developed into a process that now uses modern forming equipment resulting in superior part quality and higher production rates. Due to the application’s versatility, forging is often a great choice for operations requiring superior part strength, custom shapes and sizes, or unique performance specifications.
Custom Hydraulic Forging Presses
Beckwood’s custom hydraulic forging presses use engineering that withstands the toughest manufacturing environments like foundries and forging facilities, job shops, and everything in between. Our forging presses feature a myriad of options to accommodate all types of forging including:
- Heated and/or cooled platens
- Precise heat control
- Automated die loading and unloading
- Scrap removal systems
- Safety guarding, light curtains, and area scanners
- And more
Types of Forging Presses
Beckwood designs custom hydraulic forging presses for open and closed die forging as well as hot and cold forging. Each process has its advantages and disadvantages depending on your production needs.
Open Die Forging
Open die forging uses multiple dies which do not fully enclose the part. This process is ideal for simple shapes at lower volumes, and secondary machining is typically required.
Closed Die Forging
In closed die forging, the tooling completely surrounds the part. This allows the press to form more complex shapes at higher volumes, with little to no secondary machining required. Costs for closed dies typically run much higher than open dies, but this process results in better accuracy of the finished part.
In both of these forging processes, “flash” or excess material is a byproduct. Although, in closed-die forging the flash is less apparent because of the closed-dies, which use the flash to its advantage during the forming process.
Hot Forging
Hot forging allows for the best material deformation during the forging process because of the addition of heat. Typically, hot forging presses utilize an electric heating system which has the highest temperature capacity of all press heating methods. These higher temperatures allow for the creation of more complex geometries without straining the material. While hot forged parts can be more customized, their costs are typically higher than cold forging due to the added press features and required fixture quenching.
Cold Forging
Cold forging is best for simple shapes, high part volumes, and limited budgets. Because additional force is required to manipulate cold or ambient-temperature materials, cold forging presses typically require much higher tonnages. Cold forged materials need to have high ductility and less sensitivity to strain hardening to withstand the cold forging process without cracks and breaks.
Consult a Beckwood engineer about your hydraulic forging press needs